
COLLECTORS
Collectors can generally be classified into three categories – nonionic, anionic or cationic. Nonionic collectors are simple hydrocarbon oils. Anionic and cationic collectors consist of a polar component that selectively attaches to mineral surfaces, and a non-polar component that projects out into the solution making the surface hydrophobic. Collectors can either chemically bond to the mineral surface with high selectivity (chemisorption) or be held on the surface by physical forces (physical absorption). Collector selection is critical for effective mineral separation via froth flotation.
TIRA® manufactures customized anionic and cationic collectors for specific ore bodies and flotation process conditions primarily for the flotation of oxide ores such as phosphate and industrial minerals. Our wide range of technologies used for anionic and cationic collector formulation allow us to provide the best collector performance available. Let TIRA work with you to develop and implement a complete, customized flotation reagent package to help you succeed.

FROTHERS
The importance of frothers in mineral flotation is widely acknowledged in the mining industry. Frothers perform the following key functions in the froth flotation process:
- Reduce surface tension of the liquid-gas interface to enable froth formation.
- Hinder coalescence in order to stabilize bubble size.
- Facilitate hydrophobic particle adhesion to air bubbles.
TIRA tailor-made frothers are specially formulated blends to enhance the flotation process. They are engineered to optimize effectiveness in all types of flotation systems, especially in phosphate and other industrial mineral flotation.
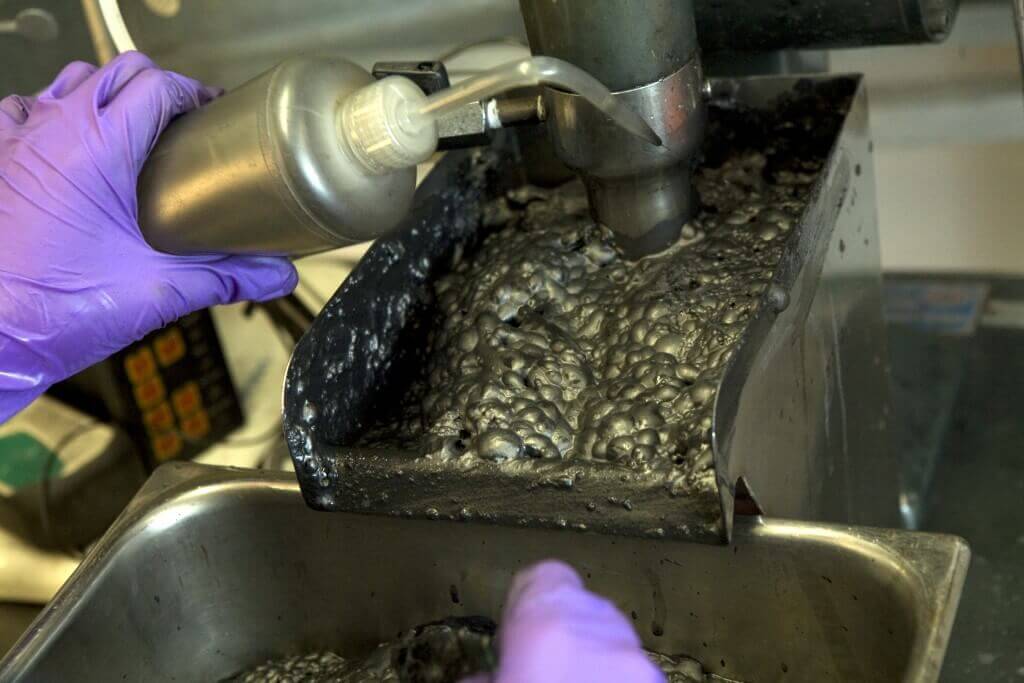
• pHMODIFIERS
Mineral conditioning and pH control can greatly affect flotation performance. Most mineral beneficiation processes require some type of pH adjustment to impart ideal separation conditions. As mineral feed quality continues to decrease, more sophisticated pH modifiers are needed to achieve optimum flotation performance. In many cases, the traditional commodity means of altering pH and the application of old chemistries do not provide the selectivity required to achieve modern mineral grade requirements. Commodity-type pH modifiers no longer deliver the best cost performance. A custom formulated pH modifier is needed to provide better froth structure and gangue selectivity for improved grade, and to create ideal conditions for increased recovery.
TIRA” S line of tailor-made pH modifiers increases the efficiency of the flotation process by facilitating optimum zeta potential and creating ideal conditions for collector function and mineral separation. They sequester soluble divalent ions which could potentially increase flotation collector usage and decrease collector efficiency, and they also help reduce the negative impact of water quality on reagent consumption. Our proprietary surfactants clean and prepare the mineral surface for efficient collector performance, and our pH modifiers selectively inhibit the interaction of gangue minerals with the flotation collector while promoting collector deposition upon the preferred mineral surface.
By precisely formulating our pH modifiers for your process we can achieve better migration of mineral-laden bubbles into the froth collection zone for a faster float, cleaner concentrate and higher mineral recovery.
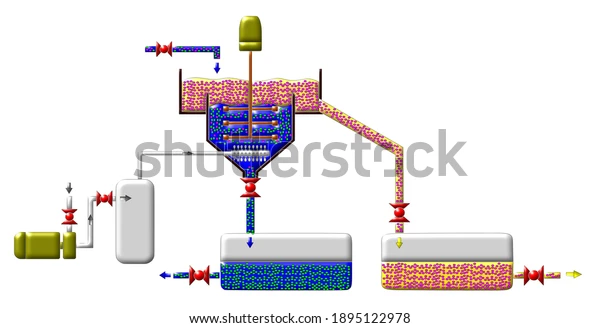
DISPERSANTS
The mining industry faces many challenges, most notably lower quality reserves. With the decreasing quality of mined feed, more sophisticated techniques are needed to achieve industry required specifications. In many cases, the typical means of altering pH or applying different chemistries is not enough to offer the mineral selectivity needed to achieve required recovery and grade goals in flotation. Depressants are often used to increase the efficiency of the flotation process by selectively inhibiting the interaction of one mineral with the collector, for example, the depression of quartzite to allow for more optimal apatite/collector interaction, thus improving final recovery and grade.
TIRA’s flotation depressants have been custom developed for a variety of applications. They help depress gangue minerals while increasing recovery and selectivity without sacrificing grade. Our depressants have been especially effective in phosphate, silica / glass sand and iron beneficiation.
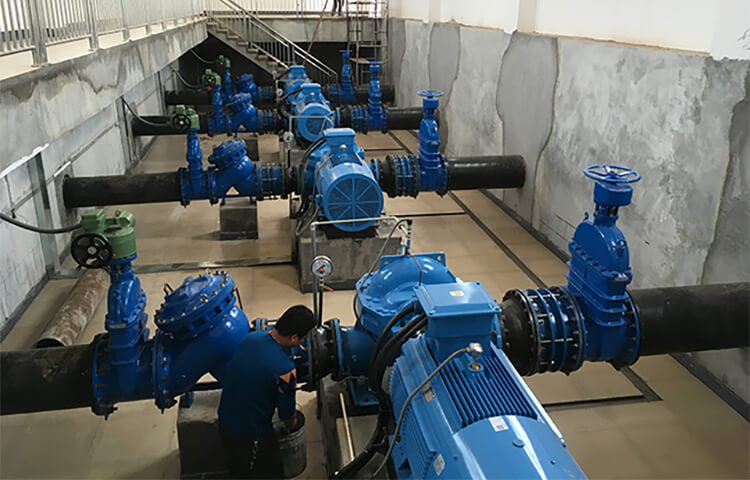
SLURRY PUMPING AIDS
Pumping mineral slurries over long distances can be very costly as a result of the energy required to move the slurry or dilution to minimize energy requirements. Slurry pumping aids such as dispersant viscosity modifiers or rheology modifiers work to reduce the rheological properties of the slurry, while allowing for increased slurry solids to be transferred over greater distances. A good example of this can be found in the transfer of phosphate concentrate to the phosphoric acid chemical plant which can be hundreds of miles away.
Rheology modifiers also assist in preventing or reducing the cementation process which can occur in the slurry pipeline due to downtime in the transportation process. A rheology modifier will allow for the slurry to redisperse upon restarting the plant, instead of cementing or compacting at the bottom of the pipeline. Some minerals require a stable dispersion for transportation in drums as they are shipped across the world. If shipped in the absence of a dispersant viscosity modifier or rheology modifier, the drums will also develop some level of cementation.
TIRA custom formulates dispersants, viscosity modifiers and rheology modifiers for specific ore types to optimize the slurry pumping process. Let us help you select, and plant test the best slurry pumping aid for your process. We will work closely with you to ensure a successful outcome for your project.
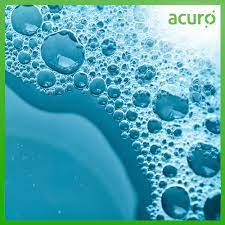
DEFOAMERS
A mining and mineral processing defoamer or anti-foaming agent is a chemical additive that can prevent, reduce, and break or remove foam and entrained gases in slurry handling equipment. It is used to slow or prevent the formation of foam, and also to break or manage foam that has already formed in mineral handling systems, especially when the foam is causing processing problems. Slowing or eliminating the formation of foam in mineral process liquids improves operational efficiency. In the mining and mineral processing fields, the terms defoamer and anti-foaming agent are frequently used interchangeably.
In mineral processes, too much foam can cause mineral losses as storage vessels foam over and equipment fills with foam, causing operational bottlenecks and slowing down mineral collection rates. Mineral processes typically encounter three types of foam challenges:
- Dissolved air in the aqueous phase
- Entrained air bubbles that are small enough and stable enough to be suspended in the slurry media
- Bubbles that have sufficient buoyancy and stability to rise to the surface and collect on top of the mineral slurry as foam.
Mining and mineral processing defoamers or anti-foaming agents can be specially formulated to comprehensively and simultaneously handle each of these challenges. Many mineral defoamers are insoluble in the foaming mineral slurry and are designed to have surface active characteristics specific to the nature of the foam, minerals and aqueous ions. A mining defoamer must act rapidly to spread across often viscous mineral foam and surfaces, breaking bubbles and foam by changing the surface tension between minerals in the aqueous phase. It attacks and interferes at the air-liquid surface where it destabilizes the foam structure or lamellae, creating a collapse or rupture of the entrained air bubbles and breaking down the surface foam. Entrained air bubbles are agglomerated into larger bubbles that buoyantly rise to the surface through the bulk mineral slurry, bursting other entrained air structures on the way up.
At the surface level of thickeners, pump boxes and other process equipment, low viscosity defoamers can spread across the surface area of the foam, bursting bubbles as the media is gently mixed to effectively remove surface foam. Eliminating these types of surface foam can reduce processing losses and help equipment run more efficiently.
In mining applications, defoamers can be enhanced by customizing the defoamer and dosing system to the application. The dosing and application of the defoamer is key to its success and a reliable and robust defoamer system is needed. In most mining scenarios, partnering with a company that custom formulates defoamers and designs dosing systems is the best approach to solve foam issues during mineral processing.
A variety of foam control agents are available to prevent the formation of foam for specific ores, mineral handling equipment, launders, and mineral pumping and flotation process conditions to aid in the handling of phosphate and industrial minerals. Lab screening of formulas and then plant testing enables the selection of the best formula for your operation. Onsite testing and process consultation can further increase value. TIRA formulates and manufactures customized defoamers for specific ore bodies, equipment types, and flotation process conditions to beneficiate oxide ores such as phosphate and industrial minerals. Let TIRA work with you to develop and implement a customized defoamer and dosing system to help you succeed.
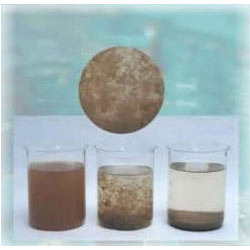
FLOCCULANTS
Flocculants are used in the mining industry to treat the water used in mineral extraction and flotation processes. They help aggregate fine suspended particles to form larger flocs so that the solids can more easily be separated from the water. Flocculants are used to clean flotation process water to reduce reagent consumption and improve recovery. They are also employed to treat discharge water so that stringent environmental standards can be met.
TIRA offers a wide range of flocculants to optimize performance for a variety of applications. Our TiraCare line of products includes: Water Clarification Aids – polymers used at mines to clean, muddy water to allow for recycling and/or environmentally acceptable clean water discharge Clay Settling Aids – polymers that enable dispersed clay to consolidate faster, allowing clean water to be recycled back to flotation plants Phosphate Rock Slurry Thickening Aids – polymers used to increase phosphate rock slurry concentrate grade prior to use in the phosphoric acid reactor.
TIRA’s technical experts will work closely with you to select the best flocculant for your application. In addition, we can provide polymer make-down, feed and metering equipment when required. Dispersants and coagulants are also available to meet your specific needs.
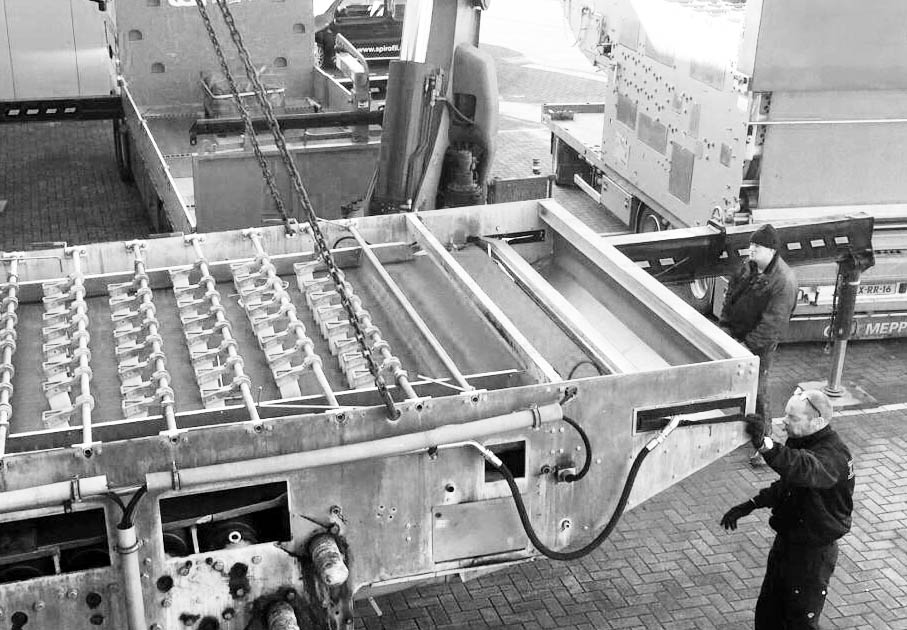
DEWATERING/FILTER AIDS
Mine dewatering / filter aids are specially formulated surface-active agents that help reduce the moisture content of mineral concentrates during filtration and subsequent storage applications. These products normally reduce the surface tension of water so that water is easily removed from mineral surfaces during filtration and storage. Dewatering / filter aids are widely used in all wet mineral processing applications where improving moisture content of filtered cakes is desired. Application areas include both sulfide and non-sulfide minerals processing and as well as coal cleaning.
Dewatering / filter aid dosage requirements vary widely based on the application. Dewatering / filter aids can be applied neat or in diluted form and points of application in the process must be carefully selected. It can be added to spray water applications onto filter cakes during filtration so that filter wash efficiency is improved or added directly into the mineral or concentrate slurries going to filtering processes and even to centrifuging.
TIRA offers various mine dewatering / filter aids for different dewatering applications. Our filter aids improve mineral concentrate filtration for better filtration efficiency, and our dewatering aids reduce the moisture content of mineral concentrates resulting in improved drying of concentrate for storage and transportation. These products also improve water recovery and water efficiency in wet mineral processing applications.
TIRA’s expert field personnel are available to our customers’ engineers, production managers and operations personnel as process advisors for dewatering applications. We will examine your mineral dewatering needs and filtration system from beginning to end and develop the best chemistry and application system to improve your operational efficiency.