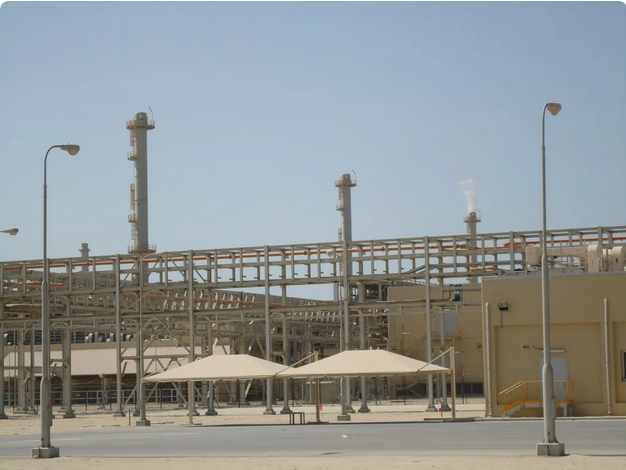
DEFOAMERS
Wet-process phosphoric acid production generates significant amounts of foam and undesirable gases which limit plant production efficiency. In a typical wet-process phosphoric acid process, phosphate rock is reacted with sulfuric acid in large digesters or reactors. In addition to the calcium phosphate in the ore being converted to phosphoric acid (P2O5) and calcium sulfate (gypsum), there are numerous side reactions due to impurities in the rock.
Carbon dioxide (CO2) content in the rock is a major contributor to foam and gas generation in the reactor. Significant foam presence on the liquid surface can lead to fugitive emissions from the reactor, overflows during start-up or upset conditions, and P2O5 loss to the exhaust gas scrubbing system. The entrained gases diminish the pumping efficiency of the system, and the foam itself takes up valuable head space in the reactors, effectively reducing production capacity. Both problems wreak havoc on the designed process parameters of the system which can result in more rapid scale formation in piping and plugging of filter media, both of which can lead to more shutdowns. When excess entrained gas and foam cause problems with sulfate control in the reaction due to poor circulation, there can also be losses of the valuable P2O5, partly due to poor gypsum crystal formation which reduces acid filtration rates.
When certain impurities are present in the phosphate rock, either organic or inorganic, they act as surfactants and tend to stabilize the gases that are released in the rock / sulfuric acid reaction, making surface foam more stable and difficult to control, and limiting the ability of the gases to disengage from the reactor slurry. When the resulting gases are entrained in the slurry, they decrease agitation and circulation by lowering pumping and mixing efficiencies, and ultimately result in lower raw material recoveries due to P2O5 carryover into flash coolers and evaporators. More detailed technical information on these mechanisms is available in a paper entitled When Nameplate Is Not Enough—Expanding Phos Acid Capacity with Defoamers. Contact us to request a copy of this paper.
One of the major challenges that phosphoric acid producers face in achieving desired plant production rates and efficiencies is identifying the optimal means of removing such gases that are liberated during these production processes. Mechanical equipment can be added to plants for this purpose but is capital intensive to install, equally expensive to maintain and provides only a partial solution at best. Process chemical additives such as defoamers have become the universally accepted “best practice” alternative for accelerating the removal of unwanted gases and improving plant performance.
The addition of a defoamer during phosphoric acid production can facilitate higher capacity utilization and optimal output of finished product. An ideal phosphoric acid defoamer not only has the ability to “knock down” surface foam in the digester but also to reduce entrained CO2 gas bubbles in the slurry. Design and choice of an appropriate defoamer requires an understanding of the characteristics of the phosphate rock, the particular type of phosphoric acid production processes and the intended operating parameters.
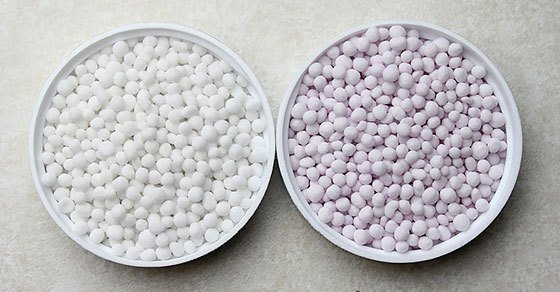
DUST CONTROL COATING
Dry fertilizers are inherently dusty products. During fertilizer production, storage, transport and use there is often significant generation of dust as particles degrade. Handling and application equipment can cause breakage, while temperature and humidity swings can cause a loss of granule integrity even while fertilizer is in storage. In some cases, imperfect production processes can result in overly fragile fertilizer which tends to partially deteriorate into dust at any given stage in the fertilizer process.
Not only is there a loss of valuable product as dust drifts away from its intended location, but dust also creates significant air quality issues. To combat this problem, dust control coatings have long been applied to fertilizers at various stages between production and application.
Appropriate fertilizer dust control coatings must:
- Provide robust, long-lasting dust control
- Have minimal impact on the flowability of the treated fertilizer
- Be made of ingredients suitable for safe use in the facilities where they are applied as well as for all downstream uses and applications including agriculture
- Not undermine the treated fertilizer’s ability to comply with applicable regulatory requirements
- Enhance the treated fertilizer’s marketability
- Be economical.
TIRA® offers a broad range of fertilizer dust control coatings in its TiraTreat & TiraCare product lines which meet all of the requirements identified above. Coatings in these lines can contribute additional benefits to the fertilizer of caking control and/or coloration. TiraTreat and TiraCare product lines can help fertilizer producers and those that handle fertilizer meet their environmental, health and safety goals. When a supplier can go to market with an appropriately treated fertilizer product, they will realize the full market value for their product while minimizing the potential for quality claims. TIRA® will help you select the best product for dust control coating and design an optimal coating application system to meet your fertilizer dust control needs.
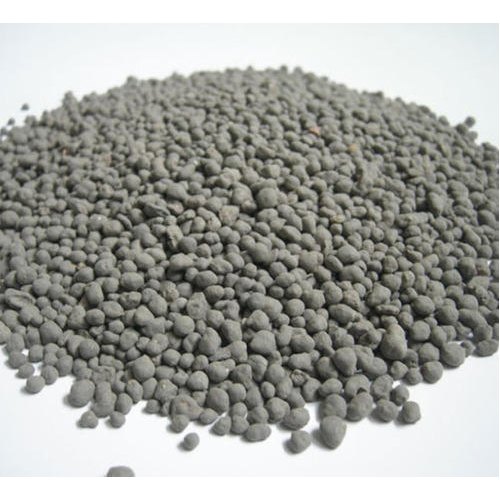
ANTICAKING AGENTS
Caking or clumping is a significant concern in dry fertilizer production, storage, transport and application. Crystallization of water-soluble salts and the resulting bridges between the surfaces of fertilizer particles is a common mechanism that causes caking. Pressure from storage conditions can also cause the surface of fertilizer particles to experience plastic deformation, causing their new contact surfaces to experience adhesion from reduced water vapor pressure.
Regardless of the cause, fertilizer caking can be highly problematic. Fertilizers are often stored in open bins in very large bulk quantities and caked product can cause portions of the pile to form unstable “cliffs” of material. Such “cliffs” can be extremely hazardous for operators of mobile equipment digging into the base of a pile since those higher, caked sections of the pile can become dislodged and tumble down like an avalanche. Caked fertilizer in bulk transport equipment can also be difficult to load and unload. It can cause improper distribution in blending or other compounding operations and can damage handling equipment. And when fertilizer is not free flowing, there will be uneven distribution during field application. All of these situations can diminish and sometimes even destroy the value of fertilizer, and in some cases, create safety hazards for workers in the industry.
Conditioning treatments for fertilizers may be used to interrupt these caking tendencies, thereby enhancing the product’s value and handling safety. Fertilizer producers can apply an external treatment of an anti-caking agent which contains appropriate surface active agents to disrupt typical fertilizer caking mechanisms. These coatings are usually formulated with other components that reduce the formation of dust, excessive amounts of which can promote crystal bridging which also contributes to caking.
Appropriate fertilizer anti-caking agents should: • Provide robust, long-lasting caking control • Be relatively easy to apply to dry fertilizer in a typical operation • Be made of ingredients suitable for safe use in the facilities where they are applied as well as for all downstream uses and applications including agriculture • Not undermine the treated fertilizer’s ability to comply with applicable regulatory requirements • Enhance the treated fertilizer’s marketability • Be economical. When producers treat their fertilizer adequately with a high-quality anti-caking agent which meets these requirements, such as those in TIRA® ’s product lines, they can be comfortable knowing that they’ve properly addressed fertilizer caking-related safety concerns in their workplace as well as in downstream handling facilities. And when a supplier is able to go to market with an appropriately treated fertilizer product, they will realize the full market value for their product while minimizing the potential for quality claims. TIRA® will help you select the best anti-caking agent and design an optimal coating application system to meet you fertilizer anti-caking needs.
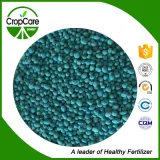
COLORING AGENTS
Today there is increasing demand for granular fertilizers which have a favorable appearance. One of the more obvious appearance differentiators is color, and so fertilizer producers need solutions to impart the desired colorations the market demands for their products. TIRA® has developed a broad range of coloring agents based on dyes and/or pigments to treat the entire fertilizer granule from the inside out, including color coatings which can further modify the color, sheen and translucency of the granule surface as desired. In addition, TIRA® ’s coating agents, which also contribute dust control and caking control, can be customized to impart color to the surface of the substrate. Our research scientists, with the help of our field technicians, can diagnose and prescribe the appropriate colorant, coating agent or, in some cases, a combination or package of multiple coloring agents to achieve the desired result for our customers.
TIRA® also designs and installs optimal application systems for our coloring agents. These application systems can be designed to include colorimeters to detect subtle changes in shade and intensity of the colored fertilizer and to synchronize these detection devices to dosing controls in order to maintain consistent adherence to color specifications.
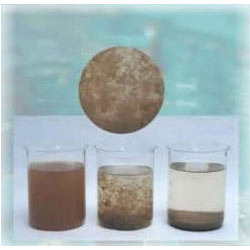
FLOCCULANTS
Flocculants are used in the mining industry to treat the water used in mineral extraction and flotation processes. They help aggregate fine suspended particles to form larger flocs so that the solids can more easily be separated from the water. Flocculants are used to clean flotation process water to reduce reagent consumption and improve recovery. They are also employed to treat discharge water so that stringent environmental standards can be met. TIRA® offers a wide range of flocculants to optimize performance for a variety of applications. Our TiraFloc line of products includes:
• Water Clarification Aids – polymers used at mines to clean muddy water to allow for recycling and/or environmentally acceptable clean water discharge
• Clay Settling Aids – polymers that enable dispersed clay to consolidate faster, allowing clean water to be recycled back to flotation plants
• Phosphate Rock Slurry Thickening Aids – polymers used to increase phosphate rock slurry concentrate grade prior to use in the phosphoric acid reactor.
TIRA® ’s technical experts will work closely with you to select the best flocculant for your application. In addition, we can provide polymer make-down, feed and metering equipment when required. Dispersants and coagulants are also available to meet your specific needs.

ANTISCALENT
Scale accumulation is a longstanding problem in phosphoric acid production processes. The large quantities of undissolved & dissolved species present during the concentration & digestion process lead to formation of scale deposits on:
- Pipelines carrying the acid Filtration systems Evaporators Heat exchangers & coolers
- Frequent plant shutdown due to necessary cleaning
- Plugging of equipment
- Inefficient feed rate to the evaporators
- Increase of pressure requirements
- Loss of P2O5 production
- Increase in maintenance and operational costs (utility costs)
- Downgraded products from lower concentration (poor heat transfer)
TIRA® Antiscalent has delivered significant benefits at various points in the process including a 90% reduction of scale mass in process piping and filtration systems. Safe-to-use and environmentally friendly Antiscalent

CLARIFICATION AIDS
During phosphoric acid production, clarification processes are used to remove contaminants from the acid. The settling rate of solid particles in the phosphoric acid clarification area closely follow theoretical laws and is often not fast enough to maintain optimum production rates in fertilizer plants or other downstream applications. In order to maximize plant efficiency, polymers such as TIRA® clarification aids are added to accelerate settling time. TIRA® ’s polymeric clarification aids are tailor-made to significantly reduce the amount of time required to remove impurities from phosphoric acid once it leaves the production process. They remove more impurities faster, for a higher quality phosphoric acid and improved downstream fertilizer grade. TIRA® clarification aids deliver significant benefits for 25-54% strength acids. Our technical experts will work closely with you to select the best aids for your clarification process.

GRANULATING AID OVERVIEW & PRODUCT DESCRIPTION
With fertilizer's oversupply globally, fertilizer producers are facing the fierce of price competition which narrowed their profit space. Fertilizer yield, production cost, productivity, uniform size, spherical shape, enough hardness, low caking tendency become the important competitive advantages. Because many factors are involved during production such as raw material variation, equipment performance, operator’s skills, productivity and physical quality are restricted and cannot be maximized. TiraMax® F200 is a specifically designed fertilizer slow-release agent that can maximize the fertilizer yield under the existing process, equipment and operation. TiraMax® F200 has superior wetting and binding properties that can largely increases coordination points, binding and the strength of agglomerates at unchanged processing conditions, which result in higher granule size output, higher agglomerate density, and higher hardness, resulting in lower deformation and disruptive forces during drying, and therefore higher chances of granule survival.
ADVANTAGES
- Uniform granules size and improved granules appearance. Reduced dusts and fines.
- Reduced caking.
- Low recycle / recirculation.
- Slow-release agent, maximizes fertilizer yield.
- Reduced steam/water consumption in granulator by 10% - 30% and therefore reduced drying energy consumption and production cost.
- Lower dependency on equipment performance and
- operator’s skills.
- Ecological and environmentally friendly.
- Multi-micronutrients, Ca, Zn, Mo, etc., helpful to crop
PRODUCT TRIAL DETAILS
The Granulating Aid is dosed into the Granulator using a metering pump at a dosage level of 2 kg to 3kg per MT of fertilizer manufactured. Before starting the dosing of Granulating Aid please collect the Granulation Data as follows:
- Plant Load MT per Hour
- Sieve Analysis of the Fertilizer produced
- Average Crushing Strength of Granules
- Dusting in Plant (Visual Observation OR Measurement of Airborne Dust Particles using the Dust Particle Monitor)
- Recycle Ratio
- Moisture Content
Dosing System:
The dosing system for the application of Granulating Aid consists of a Dosing Tank connected with a Metering Pump and the discharge end is connected with a Spray Nozzle as shown in the diagram. For temporary arrangement the Metering Pump suction can be directly inserted into the Drum to suck the Granulating Aid and pump it to the Granulator. After collecting the initial data start dosing the Granulating Aid as per the recommended dosage. The dosage of the Granulating Aid should be at the feed end of the Granulator. Preferably if it can be added along with the water of granulation, it will be better as it can easily blend with the ingredients of the Granulator well. For process plant also it can be added along with the water inlet or can be sprayed inside the granulator using compressed air. The application of the Granulating Aid should be such that maximum coverage of the ingredients inside the Granulator should take place. After the dosing of Granulating Aid is started start collecting the samples for analysis after a minimum of 4 hours. During this time the entire mass of fertilizer in the system including the recycled material will be mixed with the Granulating Aid and from 5th Hour the results can be indicative. A 3-day trial on round the clock basis will give a clear picture on the overall benefits achieved by using Granulating Aid in the plant.